Saving costs in straddle carrier operations requires a strategic approach that optimizes various aspects of the operation, including equipment maintenance, fuel efficiency, productivity, and labor utilization. Straddle carriers are essential equipment in container terminals and ports, used for lifting and transporting containers between storage yards and ships. By implementing cost-saving measures, terminal operators can enhance their competitiveness, improve profitability, and maintain sustainable operations. In this comprehensive guide, we’ll explore several strategies for saving straddle carrier costs effectively.
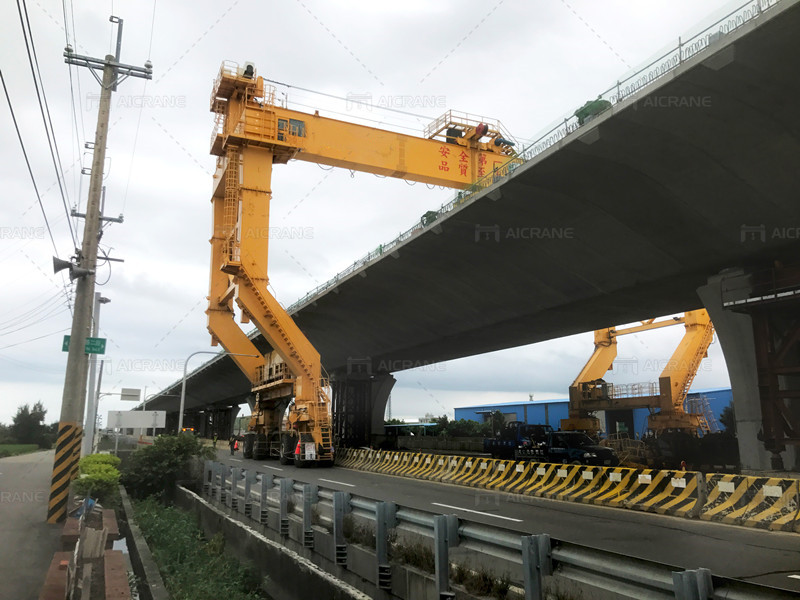
Efficient Maintenance Practices
Regular maintenance is crucial for ensuring the reliability and longevity of straddle carriers while minimizing downtime and repair costs. Implementing efficient maintenance practices can significantly reduce maintenance expenses and prolong the lifespan of the equipment. Here are some key maintenance strategies:
Preventive Maintenance: Develop a comprehensive preventive maintenance schedule based on manufacturer recommendations and industry best practices. Regularly inspect and service critical components such as engines, hydraulic systems, brakes, and tires to identify and address potential issues before they escalate into costly repairs.
Condition Monitoring: Utilize advanced condition monitoring technologies, such as vibration analysis, oil analysis, and thermography, to detect early signs of equipment wear or malfunction. Monitor key performance indicators such as engine temperature, hydraulic pressure, and fuel consumption to identify deviations from normal operating parameters and take corrective action proactively.
Operator Training: Provide comprehensive training programs for straddle carrier operators to ensure they understand proper operating procedures, equipment capabilities, and maintenance requirements. Empower operators to conduct routine inspections and basic maintenance tasks, such as lubrication and fluid checks, to prevent minor issues from escalating into major problems.
Spare Parts Management: Maintain adequate stock levels of critical spare parts and consumables to minimize downtime and delays in equipment repair. Establish partnerships with reliable suppliers and negotiate favorable pricing agreements to reduce procurement costs and lead times for replacement parts.
Fuel Efficiency Optimization
Fuel consumption is a significant operational expense for straddle carrier operations, and optimizing fuel efficiency can yield substantial straddle carrier cost savings over time. Implementing fuel-saving measures can help reduce fuel consumption without compromising productivity or performance. Here are some strategies for improving fuel efficiency:
Eco-Driving Techniques: Train straddle carrier operators in eco-driving techniques, such as smooth acceleration and deceleration, maintaining steady speeds, and minimizing idling time. Encourage operators to use engine idle shutdown features when the equipment is not in use to conserve fuel.
Equipment Tuning: Regularly tune and calibrate straddle carrier engines and fuel injection systems to ensure optimal performance and fuel efficiency. Keep engines properly maintained, including cleaning air filters, replacing fuel filters, and tuning ignition systems, to maximize fuel combustion efficiency.
Load Optimization: Optimize container handling processes to minimize unnecessary movements and maximize payload capacity per trip. Efficiently plan container stacking and retrieval sequences to reduce the number of trips and distance traveled by straddle carriers, thereby saving fuel.
Alternative Fuels: Explore the use of alternative fuels such as biodiesel or liquefied natural gas (LNG) to power straddle carriers gantry crane, which may offer cost savings and environmental benefits compared to traditional diesel fuel. Evaluate the feasibility and economic viability of alternative fuel options based on local availability, infrastructure, and regulatory considerations.
Productivity Enhancement
Improving productivity is essential for maximizing the return on investment in straddle carrier operations while minimizing per-container handling costs. Implementing productivity enhancement measures can help increase throughput, reduce cycle times, and optimize resource utilization. Here are some strategies for enhancing productivity:
Terminal Layout Optimization: Design and layout container terminals to minimize travel distances and congestion, thereby reducing turnaround times for straddle carriers. Optimize storage yard configurations, container stacking patterns, and traffic flow to streamline operations and improve efficiency.
Automation and Technology Integration: Explore opportunities to automate repetitive tasks and integrate advanced technologies such as GPS, RFID, and telematics into straddle carrier operations. Implement automated container positioning systems, remote monitoring and control capabilities, and predictive maintenance solutions to enhance productivity and reliability.
Process Optimization: Continuously review and optimize container handling processes to identify bottlenecks, inefficiencies, and areas for improvement. Implement lean manufacturing principles, such as just-in-time (JIT) scheduling, Kanban systems, and continuous improvement initiatives, to streamline workflows and eliminate waste.
Operator Training and Performance Management: Invest in comprehensive training programs for straddle carrier operators to enhance their skills, efficiency, and safety awareness. Establish performance metrics and KPIs to measure operator productivity, equipment utilization, and overall operational efficiency. Provide regular feedback and incentives to motivate operators and drive continuous improvement in performance.
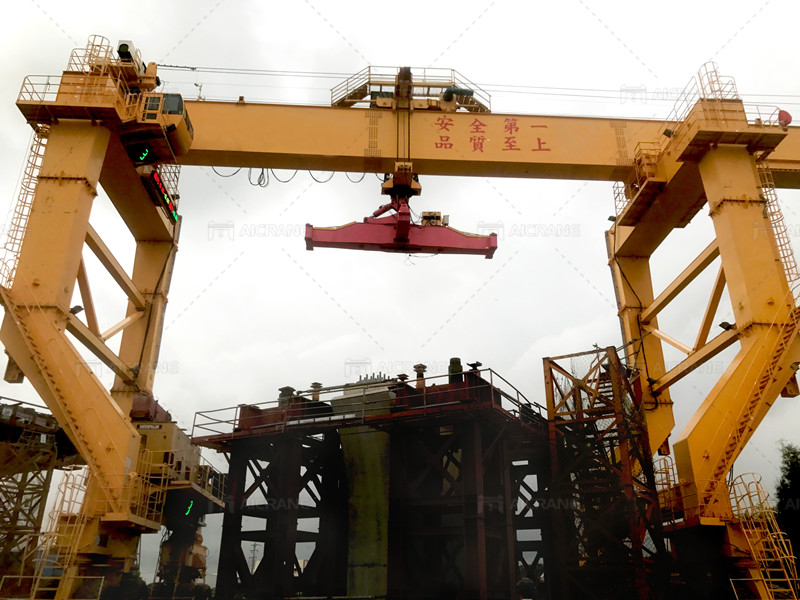
Labor Cost Reduction
Labor costs constitute a significant portion of the overall operating expenses in straddle carrier operations, and reducing labor costs can contribute to substantial cost savings. Implementing labor cost reduction measures involves optimizing staffing levels, improving workforce efficiency, and minimizing overtime expenses. Here are some strategies for reducing labor costs:
Workforce Planning: Analyze historical data, traffic patterns, and demand forecasts to develop optimal staffing schedules and resource allocations. Adjust staffing levels based on fluctuating workload volumes, seasonal demand variations, and operational priorities to minimize idle time and overtime costs.
Cross-Training and Multiskilling: Cross-train straddle carrier operators to perform multiple tasks and handle different equipment types, allowing for greater flexibility and resource utilization. Multiskilled operators can fill in for absentee or unavailable colleagues and perform additional duties as needed, reducing the need for additional staffing.
Performance Incentives: Implement performance-based incentive programs to motivate straddle carrier operators and reward productivity improvements. Tie incentives to key performance metrics such as container handling rates, equipment uptime, and safety performance to align individual and team goals with organizational objectives.
Outsourcing and Contract Labor: Consider outsourcing non-core functions or specialized tasks to third-party service providers or contract labor to reduce overhead costs associated with hiring and managing full-time employees. Evaluate the cost-effectiveness of outsourcing options based on factors such as labor rates, service quality, and contractual terms.
Maintenance Cost Reduction
Reducing maintenance costs is essential for optimizing the total cost of ownership of straddle carriers over their operational lifespan. Implementing proactive maintenance strategies and leveraging technology can help minimize downtime, repair expenses, and total maintenance costs. Here are some strategies for reducing maintenance costs:
Condition-Based Maintenance: Implement condition-based maintenance programs that leverage real-time data and predictive analytics to monitor equipment health and identify potential maintenance issues before they escalate. Use sensors, telematics, and predictive maintenance software to track key performance indicators, detect anomalies, and schedule maintenance activities proactively.
Reliability Centered Maintenance (RCM): Adopt a reliability-centered maintenance approach that prioritizes critical components and failure modes based on their impact on equipment performance and safety. Focus maintenance efforts and resources on addressing high-risk failure modes and implementing preventive measures to mitigate potential failures.
Total Productive Maintenance (TPM): Implement total productive maintenance practices to optimize equipment reliability, availability, and maintainability while minimizing maintenance costs and downtime. Engage cross-functional teams to identify opportunities for improvement, standardize maintenance procedures, and empower operators to perform routine maintenance tasks.
Spare Parts Optimization: Rationalize spare parts inventory and streamline procurement processes to minimize inventory carrying costs and reduce lead times for replacement parts. Implement just-in-time (JIT) inventory management practices, vendor-managed inventory (VMI) agreements, and strategic sourcing initiatives to optimize spare parts availability and cost-effectiveness.
Outsourced Maintenance Services: Consider outsourcing non-critical or specialized maintenance tasks to third-party service providers or original equipment manufacturers (OEMs) to reduce internal maintenance costs and leverage external expertise and resources. Evaluate the cost-effectiveness of outsourcing options based on factors such as labor rates, service quality, and contractual terms.
Continuous Improvement: Foster a culture of continuous improvement and innovation within the maintenance organization by encouraging collaboration, knowledge sharing, and process optimization. Implement feedback mechanisms, performance metrics, and benchmarking initiatives to track progress, identify opportunities for improvement, and drive sustainable cost reductions over time.
In conclusion, saving costs in straddle carrier operations requires a holistic approach that encompasses various aspects of equipment maintenance, fuel efficiency, productivity, and labor utilization. By implementing the strategies outlined in this guide and leveraging technology, best practices, and continuous improvement initiatives, terminal operators can optimize their operational efficiency, reduce costs, and maintain a competitive edge in today’s dynamic logistics environment.